Plastic extrusion for high-strength, resilient materials
Plastic extrusion for high-strength, resilient materials
Blog Article
Comprehending the Basics and Applications of Plastic Extrusion in Modern Production
In the world of modern production, the technique of plastic extrusion plays an instrumental duty - plastic extrusion. This elaborate process, including the melting and shaping of plastic via specialized dies, is leveraged throughout numerous sectors for the development of diverse products. From car parts to customer products product packaging, the applications are huge, and the possibility for sustainability is equally outstanding. Deciphering the basics of this procedure reveals truth flexibility and capacity of plastic extrusion.
The Principles of Plastic Extrusion Process
While it might show up complicated, the principles of the plastic extrusion process are based on fairly simple concepts. It is a production procedure in which plastic is thawed and after that shaped right into a constant account via a die. The raw plastic material, typically in the kind of pellets, is fed right into an extruder. Inside the extruder, the plastic is subjected to heat and pressure, creating it to melt. The molten plastic is after that forced via a designed opening, called a die, to form a long, constant item. The extruded item is cooled down and after that cut to the desired size. The plastic extrusion procedure is extensively made use of in numerous industries because of its convenience, efficiency, and cost-effectiveness.
Different Kinds of Plastic Extrusion Methods
Building upon the basic understanding of the plastic extrusion procedure, it is necessary to discover the numerous methods associated with this manufacturing approach. Both key methods are profile extrusion and sheet extrusion. In profile extrusion, plastic is melted and created right into a continual profile, usually used to develop pipes, rods, rails, and home window frames. On the other hand, sheet extrusion creates huge, level sheets of plastic, which are usually more refined into items such as food product packaging, shower curtains, and cars and truck components. Each strategy requires specialized machinery and precise control over temperature level and pressure to guarantee the plastic maintains its shape throughout cooling. Comprehending these strategies is vital to utilizing plastic extrusion properly in modern production.

The Duty of Plastic Extrusion in the Automotive Industry
A frustrating majority of components in contemporary vehicles are products of the plastic extrusion process. Plastic extrusion is mainly made use of in the production of numerous auto elements such as websites bumpers, grills, door panels, and control panel trim. Thus, plastic extrusion plays an essential duty in auto production.

Applications of Plastic Extrusion in Durable Goods Manufacturing
Beyond its considerable effect on the auto sector, plastic extrusion confirms similarly reliable in the world of customer goods making. The adaptability of plastic extrusion enables producers to make and produce intricate forms and dimensions with high accuracy and performance. The adaptability, versatility, and cost-effectiveness of plastic extrusion make it a recommended option for lots of customer goods manufacturers, adding substantially to the industry's development and innovation.
Ecological Impact and Sustainability in Plastic Extrusion
The prevalent usage of plastic extrusion in making welcomes analysis of its environmental implications. As a procedure that frequently makes use of non-biodegradable materials, the environmental influence can be considerable. Power consumption, waste production, and carbon emissions are all concerns. Industry innovations are increasing sustainability. Reliable equipment decreases energy usage, while waste monitoring systems reuse scrap plastic, reducing resources needs. Furthermore, the development of biodegradable plastics uses a much more eco-friendly choice. Regardless of these improvements, additionally development is required to reduce the ecological footprint of plastic extrusion. As society leans towards sustainability, suppliers must adjust to remain practical, emphasizing the significance of linked here continual research study and improvement in this area.
Conclusion
To conclude, plastic extrusion plays an essential duty in modern-day manufacturing, specifically in the automobile and durable goods industries. Its flexibility permits for the production of a broad array of elements with high accuracy. Moreover, its capacity for recycling and advancement of naturally degradable products supplies an appealing opportunity towards lasting techniques, consequently resolving ecological worries. Recognizing the fundamentals of this procedure is vital to enhancing its benefits and applications.
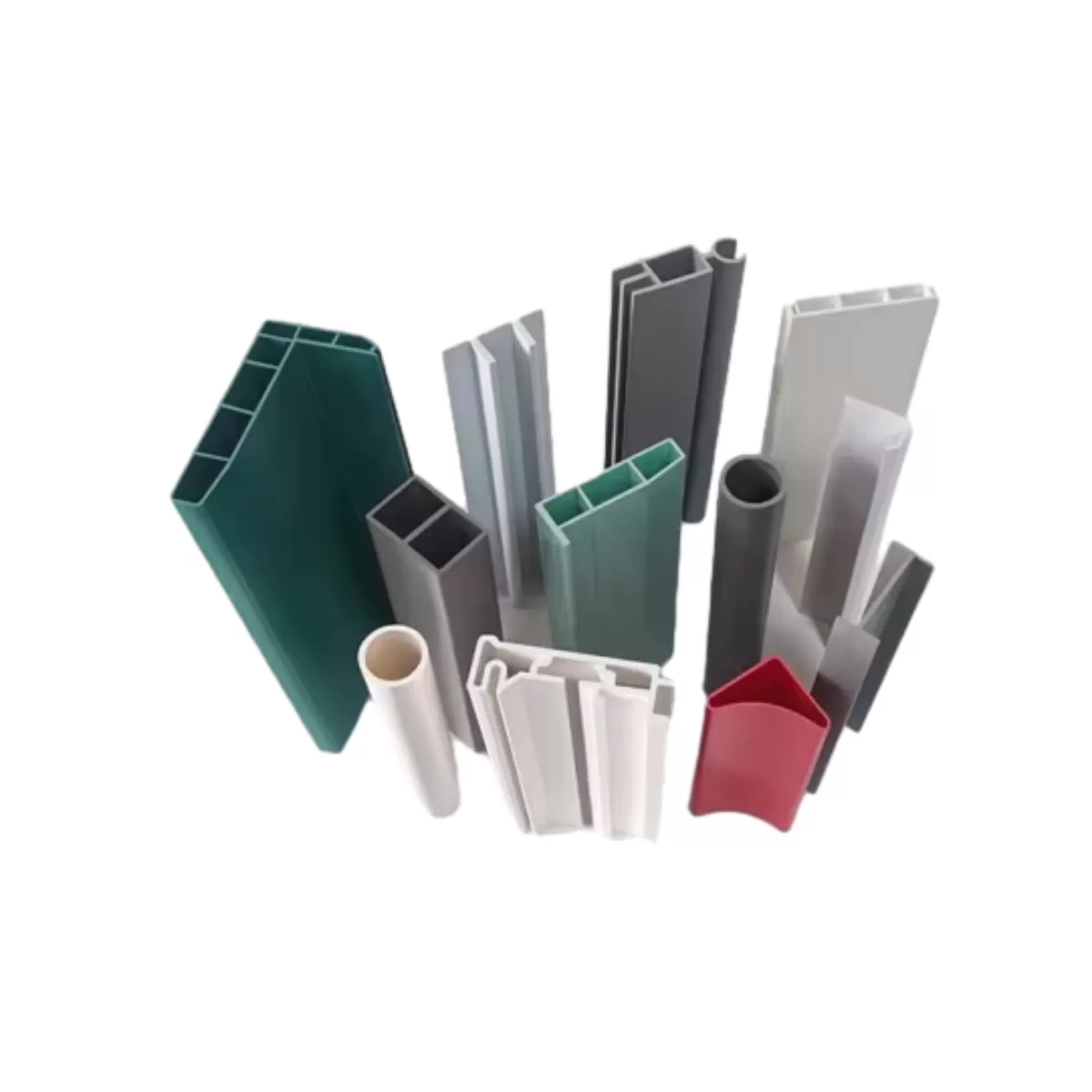
The plastic extrusion procedure is extensively utilized in numerous sectors due to its cost-effectiveness, effectiveness, and flexibility.
Building upon the standard understanding of the plastic extrusion procedure, it is essential to check out the various strategies entailed in this production approach. plastic extrusion. In contrast, sheet extrusion develops large, flat sheets of plastic, which are commonly more processed right into items such as food product packaging, shower curtains, and vehicle components.An overwhelming majority of parts in modern-day vehicles are items of the plastic extrusion process
Report this page